How Fast Do Packaging Equipment Repair Services Respond in Critical Situations?
How Fast Do Packaging Equipment Repair Services Respond in Critical Situations?
Blog Article
Uncover Just How Packaging Equipment Repair Provider Job to Keep Your Procedures Running Smoothly
Product packaging tools repair service services are crucial for maintaining the efficiency of manufacturing lines. These services not just diagnose concerns however likewise carry out required repairs to stop costly downtimes. Understanding exactly how these repairs can significantly influence functional performance. Yet, several organizations forget the signs that suggest when repair work are required. Checking out the subtleties of these solutions exposes critical insights that can help organizations stay affordable in a fast-paced market.
Recognizing the Importance of Packaging Devices Repair
Packaging equipment repair work plays a crucial role in keeping functional efficiency for businesses across different industries. The appropriate functioning of product packaging equipment is essential for ensuring that items are packaged precisely and securely, which directly influences top quality control and consumer contentment. When tools breakdowns, it can cause production delays, increased downtime, and prospective financial losses - Packaging Equipment Repair Services. Normal maintenance and punctual repairs assist to alleviate these dangers, allowing business to sustain efficiency degrees and follow shipment schedules.Furthermore, knowledgeable professionals can determine underlying problems before they escalate into substantial problems, therefore prolonging the life expectancy of the tools. This proactive strategy not only decreases repair service prices in the future but also enhances the total safety of the workplace. By prioritizing packaging equipment repair services, businesses can ensure that their operations run smoothly, ultimately sustaining their development and competitiveness on the market
Common Kinds Of Packaging Tools and Their Features
A varied array of devices is made use of in the product packaging procedure, each offering distinct functions to improve performance and item stability. One usual kind is the loading device, which properly gives fluids or solids right into containers, guaranteeing consistent quantity. Securing devices comply with, using heat or pressure to safeguard bundles and prevent contamination. Labeling makers are also crucial, as they use product information and branding, which is essential for conformity and customer acknowledgment. Additionally, cartoning devices automate the process of putting items into boxes, streamlining product packaging procedures. Stretch wrappers and reduce wrappers are used for palletizing goods, supplying security during storage and transport. Finally, examination systems ensure high quality control by detecting problems or inconsistencies in packaging. Each of these makers plays a critical function in keeping a reliable workflow, lowering manual work, and ensuring that products get to customers in optimal condition.
Signs That Your Packaging Devices Demands Repair Service
When production performance lowers or item top quality fails, it often indicates that packaging devices needs attention. Several indications can pinpoint the need for repair service. Uncommon noises, such as screeching or grinding, often suggest mechanical problems that could result in extra damage. Regular jams or misalignments during operation can interrupt operations and signal that components are put on or malfunctioning. Furthermore, irregular packaging outcomes-- such as incorrectly secured bags or mislabeled products-- can show problems with the tools's calibration or capability. A rise in downtime, needing more constant troubleshooting, is an additional sign of underlying concerns that need dealing with. Additionally, visible damage, like torn belts or rust, can endanger tools efficiency. Recognizing these indications early can stop expensive disruptions and guarantee that packaging procedures run efficiently and effectively.
The Duty of Preventive Maintenance in Packaging Workflow
Effective preventative maintenance is necessary for guaranteeing ideal performance in packaging operations, as it minimizes the threat of tools failing and enhances overall performance. By applying a structured upkeep timetable, business can determine possible issues before they intensify into considerable issues. Regular assessments, lubrication, and component replacements are vital aspects of this process, making sure that makers run at peak levels.Additionally, preventive upkeep can bring about reduced downtime, permitting for undisturbed manufacturing circulation. By addressing wear and tear proactively, organizations can expand the life expectancy of their tools and avoid expensive repair work. This strategy not only boosts performance yet also fosters a safer working setting by decreasing the likelihood of crashes triggered by malfunctioning machinery. Ultimately, a commitment to preventative maintenance is a tactical financial investment that sustains the long-lasting success and reliability of packaging operations, aligning with business objectives for performance and success.
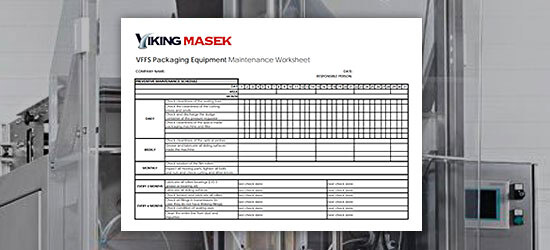
Emergency Situation Repair Providers: When Time Is of the Significance
Just how rapidly can a packaging procedure recuperate from unexpected tools failure? In such essential situations, emergency repair services play a vital duty. These solutions are designed to react quickly, typically within hours, making certain minimal downtime. Professionals are commonly check my blog on-call and equipped with the required tools and parts to address a range of tools breakdowns - Packaging Equipment Repair Services. This fast reaction is important for keeping manufacturing routines and preventing costly delays.Emergency repair service services typically include a detailed analysis procedure, allowing service technicians to identify the origin reason of the failing promptly. As soon as diagnosed, repair services can be carried out successfully, bring back tools performance. Additionally, several companies use 24/7 support, guaranteeing that assistance is readily available whenever an emergency emerges. By focusing on rapid response and expert service, packaging procedures can greatly mitigate the influence of unforeseen break downs, inevitably supporting ongoing efficiency and operational reliability
Picking the Right Packaging Devices Repair Service Provider

The Benefits of Regular Upkeep and Timely Repair Works
Regular upkeep and prompt repairs of packaging devices give substantial advantages for services. These methods not only improve equipment long life however also decrease downtime costs, causing boosted operational performance. By focusing on maintenance, business can assure smoother procedures and much better source administration.

Improved Tools Durability
While numerous companies concentrate on optimizing efficiency, disregarding routine upkeep and timely fixings can lead to raised prices and devices failings. Normal maintenance is vital you can check here for extending the life-span of packaging devices (Packaging Equipment Repair Services). It enables drivers to determine and resolve possible concerns before they escalate, thereby protecting the honesty of the machinery. Prompt repair work not only recover functionality but likewise prevent deterioration that can arise from prolonged overlook. By purchasing constant upkeep, businesses can guarantee that their tools operates at peak performance, minimizing the danger of break downs. Improved equipment longevity contributes to set you back savings in the lengthy run, as it decreases the demand for regular replacements and assists keep a consistent workflow, subsequently sustaining general functional efficiency
Lowered Downtime Expenses
Efficient maintenance and prompt repair services considerably lower downtime prices for organizations depending on product packaging devices. When equipment experiences unforeseen failures, the economic impact can be substantial, impacting production routines and revenue margins. Routine upkeep assists recognize prospective issues prior to they escalate, making sure that tools operates efficiently and continually. By addressing small fixings without delay, services can avoid pricey disturbances and mitigate the threat of prolonged downtime. This proactive method not only supports a stable process but likewise fosters a foreseeable operational budget plan. Inevitably, spending in maintenance and repair work services cultivates a resistant production environment, where organizations can sustain their one-upmanship, decrease financial losses, and keep client complete satisfaction by delivering items on schedule.
Improved Functional Efficiency
Prompt repair services and consistent maintenance play an essential duty in improving operational efficiency for companies using packaging equipment. Regular upkeep warranties that equipments run at peak levels, lowering the chance of breakdowns that can interfere with manufacturing processes. When tools is well-kept, it can function more accurately, causing increased result and uniformity in product quality. Additionally, timely repairs minimize the risk of substantial damage, which typically results in costly substitutes and prolonged downtimes. By prioritizing maintenance and fixing solutions, services can improve their operations, eventually leading to price savings and improved productivity. This aggressive approach not just extends the lifespan of the tools however additionally fosters a safer working environment, adding to overall functional success.
Regularly Asked Questions
Exactly How Promptly Can I Expect Product Packaging Tools Repair Work Services to Respond?
The rate of reaction from product packaging devices repair work solutions can vary substantially. Typically, business aim to deal with immediate requests within hours, while much less vital concerns may take longer, depending upon accessibility and the intricacy of the repair work needed.
Are Product Packaging Tools Repair Solutions Available for All Equipment Brands?
Product packaging tools repair service services normally deal with different equipment brand names. Nevertheless, availability may differ based upon the supplier's experience and partnerships, making it important for operators to validate compatibility with their particular equipment before seeking assistance.
What Qualifications Should Technicians Have for Product Packaging Devices Repair Service?
Professionals concentrating on product packaging devices repair generally possess certifications in mechanical design or related fields, comprehensive hands-on experience, and knowledge of details machinery brands, guaranteeing they can efficiently detect and fix different devices problems.
Exactly How Can I Avoid Future Break Downs After Repair Services?
To avoid future break downs, routine upkeep schedules ought to be developed, operator training highlighted, and equipment surveillance carried out. These proactive steps can noticeably improve dependability and durability, lowering the possibility of operational interruptions and unforeseen repairs.
What Is the Ordinary Price of Product Packaging Equipment Fixing Solutions?
The typical price of product packaging tools fixing services differs considerably, normally ranging from $100 to $1,500, depending on variables such as devices kind, complexity of the problem, and required components or labor for the repair. Packaging equipment repair services are vital for maintaining the effectiveness of manufacturing lines. Regular upkeep and timely repair services of product packaging equipment supply substantial advantages for services. Efficient maintenance and timely repairs substantially lower downtime costs for businesses counting on packaging devices. Timely repair services and consistent maintenance play a pivotal function in boosting operational efficiency for services using packaging equipment. Product packaging tools repair solutions typically cater to various equipment brand names.
Report this page